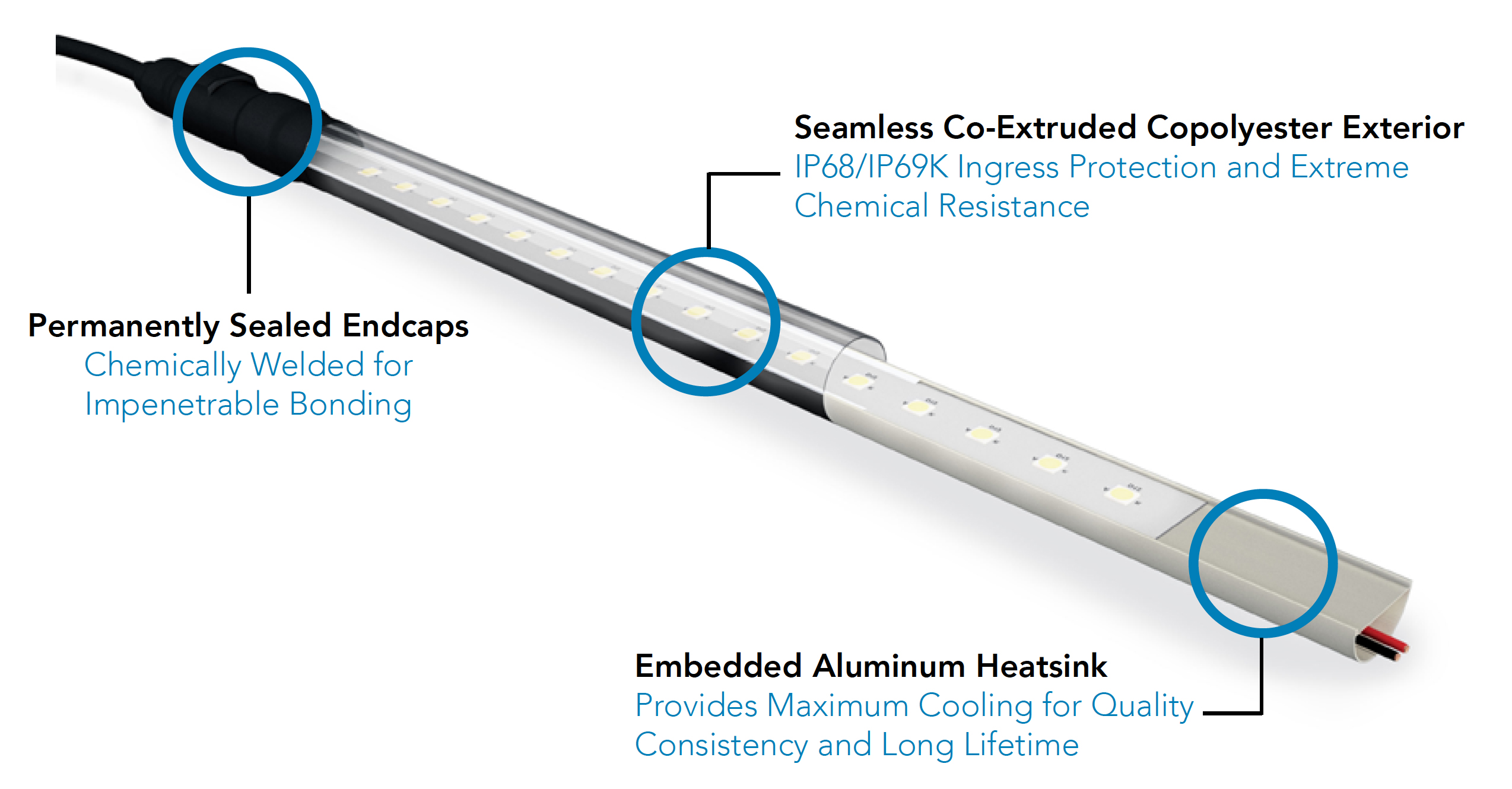
IP69K is the highest ingress protection rating available, on the IP rating scale. The first digit in ‘69’ represents the level of protection against solids, dirt, and dust. The highest level of protection for the first digit is a 6, representing no ingress of dust. The second digit is protection from liquid ingress, including water. The highest value is a 9, which is protection against steam-jet cleaning. The ‘K’ specifically represents ingress protection against high temperatures and high pressures. Look for IP69K for your most demanding applications.
If your new luminaire cracks from an impact, it’s probably no longer chemical resistant. Seek luminaires with an IK impact rating of at least IK07. The highest impact rating is IK10. IK10 protects against the impact of a 5 kg (~ 11 lbs) mass dropped from 200 mm (~ 8 inches) above the impacted surface. This represents a 20 joules impact. Ignoring the IK rating means your new fixture could become compromised with its first impact.
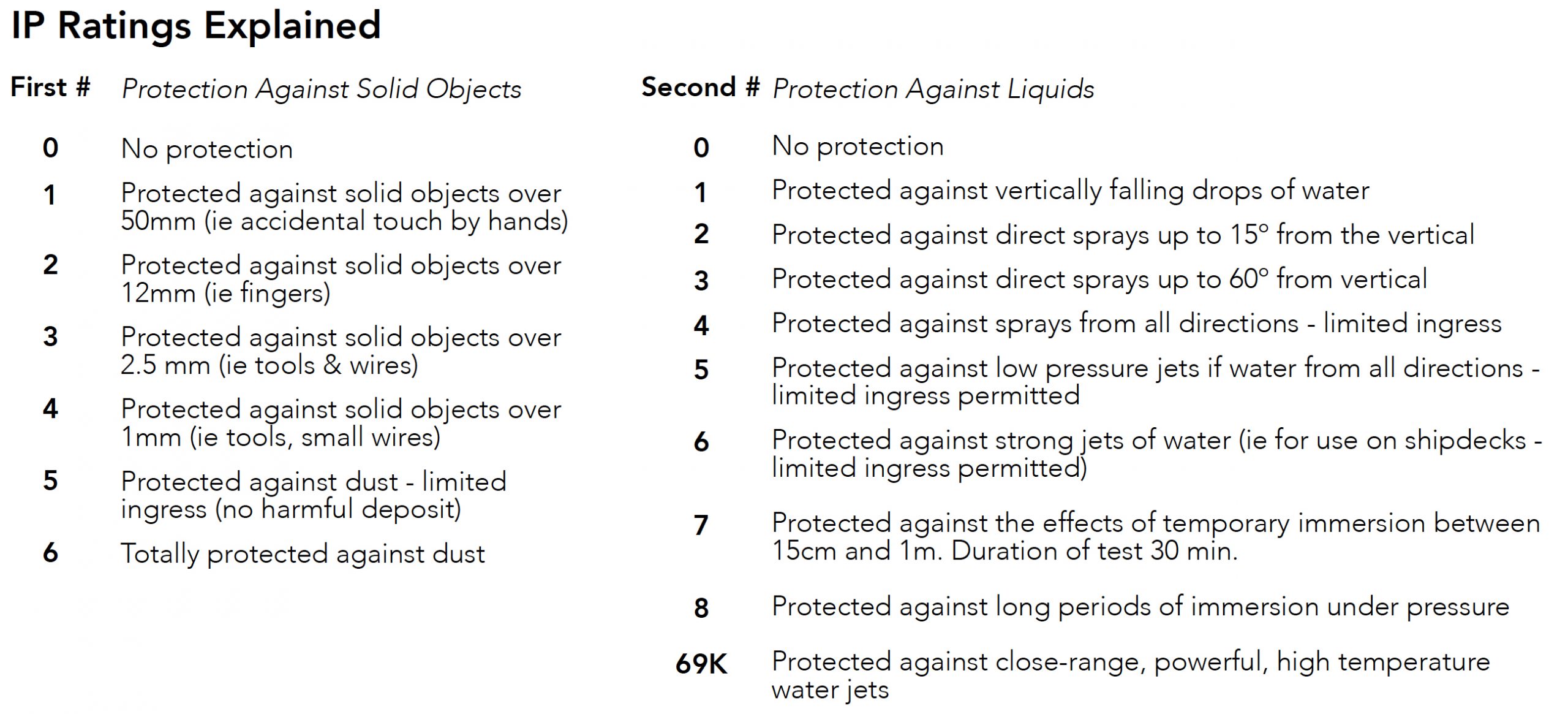
Corrosion resistance is one form of chemical resistance. Corrosion resistance is how well a substance (especially a metal) can withstand damage caused by oxidization or other chemical reactions. Preventing rust or other oxidation of metals is an important aspect of chemical resistance. A copolyester, fully-sealed co-extrusion protects any internal metals, such as aluminum, solder, and metal fasteners, from oxidation or rust.
Thermal Management for Sealed Fixtures
Completely sealing up a fixture to keep out dust, water, and chemicals also has the potential to trap more heat from the LEDs and power electronics. A quality luminaire design will utilize conduction of heat as a strategy to move heat out of a sealed luminaire. This can be accomplished with the aluminum + polymer co-extrusion. Aluminum is an excellent conductor of heat, and much better than steel. It’s also possible for the copolyester polymer to have carbon fillers added to increase its thermal conductance and protect all of the LED and power electronics from heat buildup. Make sure any manufacturer that you consider has thought through the thermal management implications of a highly-sealed luminaire, and has optimized conductive heat flow out of the fixture.